There are a variety of battery technologies available at the present and as such we will use a method similar to that used to determine the proper solar panel technology, along with a pro/con list to determine the optimal battery type. The following batteries were chosen as a representation of the current state of the industry for each battery type.
Battery Specifications
Battery | Voltage (V) | Charge Storage (Ah) | Mass(kg) | Volume(m3) |
LEAD ACID 12V 120AH BP120-12-ND | 12.0 | 120.0 | 39.500 | .01682000 |
BATT NIMH 1.2V D 6500MAH | 1.2 | 6.5 | .175 | .00005380 |
BATT NICAD 1.2V F 7000MAH | 1.2 | 7.0 | .224 | .00007374 |
Tenergy Li-Ion 26650 3.7V 4200mAh | 3.7 | 4.2 | .094 | .00003630 |
Polymer Li-Ion Cell: 3.7V 10Ah | 3.7 | 10.0 | .196 | .00008280 |
The following figures of merit are derived from the specifications in the previous table. These are used as a simple way of comparing important capabilities of the batteries.
- Energy Storage Cost: This metric determines how costly it is to store energy is each battery type. Lower values are better.
- Specific Energy: This metric determines how much energy is stored for an amount of weight in each battery type. Higher Values are better.
- Energy Density: This figure determines how much energy is stored for an amount of volume in each battery type. High values are better.
Battery Figures of Merit
Battery Technology | Energy Storage Cost ($/Wh) | Specific Energy (Wh/kg) | Energy Density (Wh/m3) |
Lead Acid | .20 | 36.460 | 85612.4 |
NiMH | 1.39 | 44.570 | 144981.4 |
NiCAD | 1.62 | 37.500 | 113913.8 |
Li-Ion | .64 | 165.320 | 428099.2 |
Li-Polymer | .73 | 188.775 | 446859.9 |
Battery Pro/Cons
Battery Technology | Pros | Cons |
Lead Acid | -Inexpensive -Low Maintenance -Low Self Discharge | -Low Energy Density -Should not be deeply discharged |
NiMH | -Higher Capacity than NiCd | -High Maintenance (Periodic Full Discharge) -Not as Rugged as NiCd (Temperature, More Complex Charging) -Limited Deep Cycle Life |
NiCd | -Very Rugged (Temperature, charge cycle, Shelf Life etc.) -Fast Charge | -Low energy Density -High Self Discharge |
Lithium Ion | -High Energy Density -Low Self Discharge -Low Maintenance | -Cost -Protection circuitry required |
Lithium Polymer | -Lightweight -Similar to Lithium Ion in characteristics | -More expensive than Lithium Ion |
With this data in hand we must construct a set of requirements to judge these batteries on based on our specific project parameters. Our battery must be able to have a high capacity, a “set and forget” maintenance schedule, and be reasonably light. The capacity must be enough to run the charging station for at least 12 hour with no help from the solar generator with solar panels. This does not mean that the charging station must run at full draw for 12 hours. At a full draw of 180W for 12 hour the battery must have 2160Wh of energy storage. This is the “worst case” scenario for our product, and an unreasonable requirement for any battery storage system of this scale. More realistically the charging station will not be in full use for a complete 12 hours. We will use an “average use case” of charging one laptop and one cell phone per two hour. We will assume about 7Wh of energy for the cell phone and 60Wh for the laptop. This totals to 402Wh total for our goal.
Using the 402Wh figure we can determine the specifications for the battery we will require.
Battery Technology | Cost ($) | Weight (kg) | Volume (m3) |
Lead Acid | 80.4 | 11.02 | .00470 |
NiMH | 558.78 | 9.02 | .00280 |
NiCAD | 651.24 | 10.72 | .00350 |
Lithium-Ion | 257.28 | 2.43 | .00094 |
Lithium-Polymer | 293.46 | 2.13 | .00090 |
If we look only at the cost the lead acid technology seems to win out with a cost many times lower than the competition. The lead acid technology is however the largest and most heavy out of all the contenders. At 11kg and almost 5 liters it would be difficult to elegantly integrate into the design of the charging station and still allow a reasonable degree of portability. The NiCAD and NiMH technologies are immediately out of the running as their metrics are worse in every way compared to the lithium technologies. There is a small benefit to the lithium polymer technology over the traditional lithium ion; however in this application the difference is too small to justify the increased cost. Thus the lithium ion technology is the correct choice for this application.
Selecting a Lithium Ion Battery and Protection Circuits
There are a few things to think about when selecting a battery or set of batteries. The main considerations are capacity and maximum discharge current. Our application requires both high capacity and high current.
We expect the power draw of the loads to be about 144W to place a buffer on this value we will design for a maximum value of 180W. Lithium Ion cells typically have a voltage of 3.7v per cell. One cell delivering this power would mean that the total current draw from the battery would be 48.6A. This high value is due to the very low cell voltage. A typical “Fast Discharge” value for a lithium ion cell is about 2A. To lower the required current these cells can be placed in series increasing the total voltage. The minimum number of cells used in this way can be calculated by 180𝑊/2𝐴 = 90𝑉, 90𝑉/3.7𝑉 = 24.3
This means that if connected in this way at least 25 cells must be placed in series at the input of the DC/DC and DC/AC converters. This is not the only method do decrease the current draw through the individual cells. Multiple parallel stacks of cells can divide the required current between them. It is important to note that when dealing with individual lithium ion cells that the output must run through protection circuitry. Lithium ion chemistry is delicate and can be easily damaged by overcharge or over discharge. Another consideration that the protection circuitry prevents is the discharge of one cell into another. If one cell happens to be at a higher voltage than another it may discharge to equalize the voltage. If the batteries are being used to power something at the time the total current from the solar battery could rise to very high levels. The protection circuitry prevents this by monitoring the current through each stack of cells.
A review of the available options for lithium ion batteries revealed that the LiFePO4 chemistry is ideal for out project. LFP (Lithium Iron Phosphate) cells are much safer than standard LiCoO2 cells with a much smaller chance of combustion when mishandled. LFP cells have an extremely long cycle lifetime compared to LiCoO2 cells (LFP cells have a lifetime of higher than 2000 cycles, while LiCoO2 cells have a lifetime of around 500 cycles). The solar generator of ATO solar generator equipped with lithium battery, it will be more economical for consumers if the batteries don’t need to be replaced, so this metric is very important. In addition LFP cells have a much higher power density when comparted to other Lithium chemistries. With the high peak amount of power out product needs to deliver when “fully loaded” this is a very important consideration.
The disadvantage of LFP cells comes from their energy density which can be up to 40% less than LiCoO2. While the weight and size of our product is very important the difference between these two chemistries is not enough to outweigh the advantages of LFP cells. LFP cells still are more energy dense than any other battery type outside of lithium ion.
With a necessary minimum fully charged energy of at least 402Wh we selected a set of four LFP cells which with 128Wh for a total of 512Wh. At a cost of $240 with set comes to $0.47/Wh, which is actually under our initial estimates for the total cost and cost per Wh of a LiIon Battery Solution. In fact $0.47/Wh approaches the $0.20/Wh of the lead acid technology.
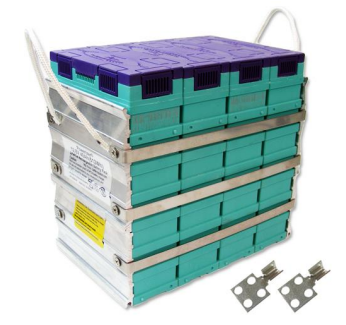
This particular set of cells has a recommended battery protection unit which meets all of our specifications. This protection unit has over and under voltage protection for each individual cell, as well as overcurrent protection which is even more conservative than the recommended maximum current specification of the cells, yet still meets the maximum current needs of our application. The price point of $29.95 in addition to the four LFP cells puts the total cost of the battery system at $270. This is within the expected values for this portion of the Solar Charging Station.
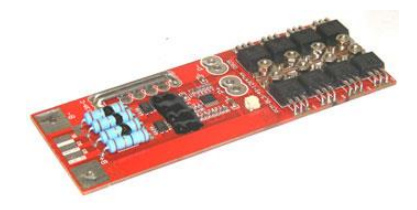